Design factors that influence the thermal performance of a heat sink
When selecting or designing a heatsink the following factors must be considered:
- Thermal resistance
- Material
- Fin efficiency
- Spreading resistance
- Fin arrangements
- Surface colour
What is a heatsink?
In electronic systems, a heatsink is a passive component that cools a device by dissipating heat into the surrounding air. Heatsinks are used to cool electronic components such as high-power semiconductor devices, and optoelectronic devices such as higher-power lasers and light-emitting diodes (LEDs). Heatsinks are heat exchangers such as those used in refrigeration and air conditioning systems, or the radiator in an automobile.
How does a heatsink work?
A heatsink is designed to increase the surface area in contact with the cooling fluid surrounding it, such as the air. Approach air velocity, choice of material, fin (or other protrusion) design and surface treatment are some of the factors which affect the thermal performance of a heatsink.
Where are heatsinks used and how are they attached?
Heatsinks are used to cool computer central processing units (CPUs) or graphics processors. Heatsink attachment methods and thermal interface materials also affect the eventual die temperature of the integrated circuit. Thermal adhesive or thermal grease fills the air gap between the heatsink and device to improve its thermal performance. Theoretical, experimental and numerical methods can be used to determine a heatsink's thermal performance.
Surface Colour
The heat transfer from the heatsink occurs by convection of the surrounding air, conduction through the air, and radiation. Heat transfer by radiation is a function of both the heat sink temperature, and the temperature of the surroundings that the heat sink is optically coupled with. When both of these temperatures are on the order of 0 °C to 100 °C, the contribution of radiation compared to convection is generally small, and this factor is often neglected. In this case, finned heat sinks operating in either natural-convection or forced-flow will not be effected significantly by surface emissivity.
In situations where convection is low, such as a flat non-finned panel with low airflow, radiative cooling can be a significant factor. Here the surface properties may be an important design factor. Matte-black surfaces will radiate much more efficiently than shiny bare metal in the visible spectrum. A shiny metal surface has low effective emissivity due to its low surface area. While the emissivity of a material is tremendously energy (frequency) dependent, the noble metals demonstrate very low emissivity in the NIR spectrum. The emissivity in the visible spectrum is closely related to color. For most materials, the emissivity in the visible spectrum is similar to the emissivity in the infrared spectrum; however there are exceptions, notably certain metal oxides that are used as "selective surfaces".
The vast majority of ABL Components' Heatsinks - single piece extrusion, customised extrusion, BGA and board mount - are black anodised on-site at ABL to assist performance. High powered extrusions - because of their unique manufacturing process - are not black anodised because the performance of these heatsinks has been optomised by the excellent surface area created by the high fin ratios utilised in these designs.
Fin efficiency
Fin efficiency is one of the parameters which makes a higher thermal conductivity material important. A fin of a heat sink may be considered to be a flat plate with heat flowing in one end and being dissipated into the surrounding fluid as it travels to the other. As heat flows through the fin, the combination of the thermal resistance of the heat sink impeding the flow and the heat lost due to convection, the temperature of the fin and, therefore, the heat transfer to the fluid, will decrease from the base to the end of the fin. Fin efficiency is defined as the actual heat transferred by the fin, divided by the heat transfer were the fin to be isothermal (hypothetically the fin has infinite thermal conductivity).
Equations are applicable for straight fins.
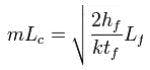
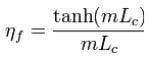
Where:
1. hf is the convection coefficient of the fin
- Air: 10 to 100 W/(m2K)
- Water: 500 to 10,000 W/(m2K)
- Aluminum: 120 to 240 W/(m•K)
4. tf is the fin thickness (m)
Spreading Resistance
Another parameter that concerns the thermal conductivity of the heat sink material is spreading resistance. Spreading resistance occurs when thermal energy is transferred from a small area to a larger area in a substance with finite thermal conductivity. In a heat sink, this means that heat does not distribute uniformly through the heat sink base. The spreading resistance phenomenon is shown by how the heat travels from the heat source location and causes a large temperature gradient between the heat source and the edges of the heat sink. This means that some fins are at a lower temperature than if the heat source were uniform across the base of the heat sink. This nonuniformity increases the heat sink's effective thermal resistance.
To decrease the spreading resistance in the base of a heat sink:
- Increase the base thickness
- Choose a different material with better thermal conductivity
- Use a vapor chamber or heat pipe in the heat sink base
Fin Arrangements
A pin fin heat sink is a heat sink that has pins that extend from its base. The pins can be cylindrical, elliptical or square. A pin is by far one of the more common heat sink types available on the market. A second type of heat sink fin arrangement is the straight fin. These run the entire length of the heat sink. A variation on the straight fin heat sink is a cross cut heat sink. A straight fin heat sink is cut at regular intervals.
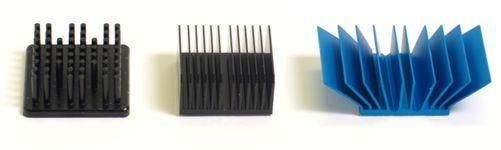
Figure 1 Pin, Straight and Flared fin heat sink types.
In general, the more surface area a heat sink has, the better it works. However, this is not always true. The concept of a pin fin heat sink is to try to pack as much surface area into a given volume as possible. As well, it works well in any orientation. Kordyban has compared the performance of a pin fin and a straight fin heat sink of similar dimensions. Although the pin fin has 194 cm2 surface area while the straight fin has 58 cm2, the temperature difference between the heat sink base and the ambient air for the pin fin is 50 °C. For the straight fin it was 44 °C or 6 °C better than the pin fin. Pin fin heat sink performance is significantly better than straight fins when used in their intended application where the fluid flows axially along the pins (see table below) rather than only tangentially across the pins.
Comparison of a Pin Fin and Straight Fin heat sink of similar dimensions. | ||||||
Heat sink fin type | Width [cm] | Length [cm] | Height [cm] | Surface area [cm²] | Volume [cm³] | Temperature difference, Tcase − Tair [°C] |
Straight | 2.5 | 2.5 | 3.2 | 58 | 20 | 44 |
Pin | 3.8 | 3.8 | 1.7 | 194 | 24 | 51 |
Another configuration is the flared fin heat sink; its fins are not parallel to each other, as shown in figure 1 above. Flaring the fins decreases flow resistance and makes more air go through the heat sink fin channel; otherwise, more air would bypass the fins. Slanting them keeps the overall dimensions the same, but offers longer fins. Forghan, et al. have published data on tests conducted on pin fin, straight fin and flared fin heat sinks. They found that for low approach air velocity, typically around 1 m/s, the thermal performance is at least 20% better than straight fin heat sinks. Lasance and Eggink also found that for the bypass configurations that they tested, the flared heat sink performed better than the other heat sinks tested.
Thermal Resistance
For semiconductor devices used in a variety of consumer and industrial electronics, the idea of thermal resistance simplifies the selection of heat sinks. The heat flow between the semiconductor die and ambient air is modelled as a series of resistances to heat flow; there is a resistance from the die to the device case, from the case to the heat sink, and from the heat sink to the ambient. The sum of these resistances is the total thermal resistance from the die to the ambient. Thermal resistance is defined as temperature rise per unit of power, analogous to electrical resistance, and is expressed in units of degrees Celsius per watt (C/W). If the device dissipation in watts is known, and the total thermal resistance is calculated, the temperature rise of the die over ambient can be calculated.
The idea of the thermal resistance of a semiconductor heat sink is an approximation. It does not take into account the non-uniform distribution of heat over a device or heat sink. It only models a system in thermal equilibrium and does not take into account the change in temperatures with time. Nor does it reflect the non-linearity of radiation and convection with respect to temperature rise. However, manufacturers tabulate typical values of thermal resistance for heat sinks and semiconductor devices, which allows the selection of commercially manufactured heat sinks to be simplified.
Commercial extruded aluminium heat sinks have a thermal resistance (heat sink to ambient air) ranging from 0.4 C/W for a large sink meant for TO3 devices, up to as high as 85 C/W for a clip-on heat sink for a TO92 small plastic case. The famous, popular, historic and notable 2N3055 power transistor in a TO3 case has an internal thermal resistance from junction to the case of 1.52 C/W. The contact between the device case and heat sink may have a thermal resistance of between 0.5 up to 1.7 C/W, depending on the case size, and the use of grease or an insulating mica washer.